How to minimize picking errors
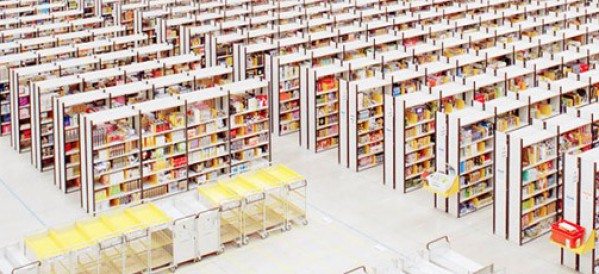
The implementation of a Warehouse Management System (WMS) using the automated module (with barcode reader) acts directly and critical points in the process, such as the separation of packages
Looking at the macro processes of a logistics operation – receiving, storing, picking and shipping – you can check for errors in the process linked to the lack of knowledge and attention.
The errors due to lack of knowledge are easier to be corrected because they can be remedied through training and operational flows settings. The error due to lack of attention is more difficult to control because it occurs due to the pressures of the internal and external environment of the organization that the employee is exposed.
In the picking process, the main errors that occur are separating the incorrect product, Stock Keeping Unit errors (SKU) different, or different logistics data, such as batch manufacture, expiration date, date of manufacture, serial number, etc. , incorrect amount of fragmentation and “forgotten” items. These problems are generally the shift change, the output and return the meal schedule.
The picking activity is the most complex warehouse, which has a direct impact on operating costs. The question for this scenario is how to minimize crashes?
The implementation of a Warehouse Management System (WMS) using the automated module (with barcode reader) acts directly on the errors mentioned above. Making use of the controller in the picking, the system validates that same item being read is requested at the time of reading the product bar code, thus preventing happen separation of incorrect objects.
In the automated process it is possible to divide the unit performing reading unit or query the product label and entering the separate amount. Still, with the implementation of WMS, you can perform the shipping conference, which is held the reading of the products after picking, validating the separated amount is correct. You can also deploy the boarding conference, checking the products being shipped in vehicles.
By default, the system requires that reading product bar codes is performed to confirm the separation. The next process, dispatch conference, you can detect the lack of the product and verify the address which was confirmed systemically separation, negating the possibility of forgetting items.
Besides helping to reduce the errors mentioned above, the use of WMS in the picking and shipping management adds to the process gains, such as routing, management of performing separation waves could be seen by the group or individual application, the possibility of packing and picking assembly in or on shipping conference, beyond the control of the serial number, and validation of the audit picking fragility index of the products on the transport assembly during separation pallete.
The process also ensures the validation of FIFO, FEFO, expiration date, pre validation of the balance (physical and tax) before starting the separation and generating shipping label. The data entry redundancy is also inhibited because there is the possibility of integrating applications by EDI’se XML electronic invoices.
Importantly, in addition to the technological apparatus, process flow definition, definition of roles and responsibilities in the process, physical organization and determination of physical space to accommodate the post picking, post conference and pre-shipment are essential for the picking process is carried out efficiently and effectively.
Also within this topic, it is noteworthy attention in receiving processes, handling and inventory, seeking to decrease the occurrence of stock breaks (physical versus systemic divergence), which are a major cause of lost time in the separation of activity.
Full article: http://cio.com.br/