The indicators X costs of logistics in Brazil
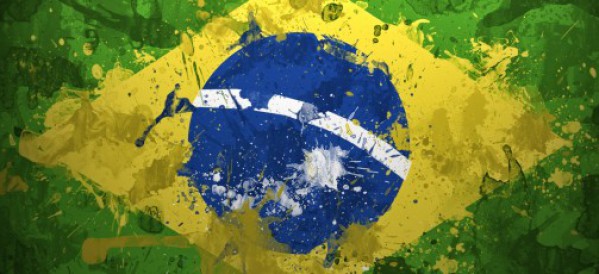
According to ILOS (Institute of Logistics and Supply Chain), spent R $ 507 billion dollars in 2013 with only logistic This number represents about 8.5% in net sales of Brazilian companies. The logistics activity that generates more costs in Brazil is transportation, followed by warehousing and storage. And when it comes to logistics costs, the major challenge is in creating a plan to reduce it in order to make the company more competitive in your field.
To do this, first you need to set the main costs within the two major logistics activities: transport and storage. The higher costs of transport are related to vehicle maintenance, fuel and tires, but must also be taken into account damage from shipping, the cost of goods in transit, theft charges, reverse logistics, among others. If transport is outsourced, will still have the cost of shipping. In the case of inventory and storage, should be considered handling costs, losses, damages, secure stockpiles, the costs generated by the warehouse (rent and administrative expenses) and the stock of fixed itself.
An effective way to identify the points that generate more costs (and bottlenecks) within the logistics process is to make use of performance indicators or KPIs (Key Performance Indicators). These indicators reflect the performance of an operation or process, providing data that can be analyzed and subsequently managed proactively, enabling managers to create a strategic plan for cost reduction and continuous improvement, focusing on problem areas.
According to Kaplan and Norton (1997), which is not measured is not managed. And with the information provided by these indicators, in addition to costs, it is also possible to reduce the execution time of tasks, improve performance, work critical points, improve the level of service, among other gains in the operation. These indicators should be measured frequently, not only to plan and control, but also in order to diagnose possible faults in the process.
But it is clear that the indicators may vary according to the area of operations, strategy and vision of each company. To obtain these indicators is necessary to have quantitative information about available resources, time processes, meeting requests, operational capacity, a result of operational tasks, quantities of documents, among many other information that can not obtained quickly and in real time through tools TMS (transportation Management System) and WMS (Warehouse management System), which are essential in the management of transport and storage.
In addition to the quantitative information provided by the technology tools mentioned above, when we will mount the indicators we have to hand in the goals and objectives of the organization as to develop strategies to leverage the operations initially consists of “knowing where we are” and “where we want to go “. The indicators generated by the WMS and TMS provided us information “where we are”, “how fast is being executed activities”, “where are the bottlenecks,” “managerial and financial views of the process.” The goal of the organization is traces the goal to be achieved for each indicator.
As the WMS and TMS basically manage the entire logistics chain, the necessary information is already on its banks and data need only be developed and presented in a way that can be analyzed quickly. These indicators should measure time and value of the most critical operations of day to day business or all of them if possible. In possession of this information is possible to measure and analyze indicators such as transportation: percentage of deliveries or collections completed on time, cost breakdowns in transportation, percentage and cost delays, use of vehicle capacity, rate of order fulfillment and accuracy in issue of CT-e (Electronic Bill of Lading).
When it comes to storage, which manages the order fulfillment rate, cycle time applications, accuracy of inventory, resource productivity in each task / process time of the vehicle at the dock, accuracy of address, use of storage capacity, cost of inventory and inventory turnover, it is possible to know the points that causes major bottlenecks in the processes and also the cause of the problem, allowing the manager to take action to reduce these bottlenecks and meets the customer in less time. You can also see where are the points that are more cost operation and treat them more appropriately. The case is that the indicators vary for each company and it is up to each manager know what should be measured to fit their needs indicators are developed.
Management tools (TMS and WMS), because they have the necessary information, as mentioned earlier, are improving to provide such indicators in the form of management reports and dashboards (graphical representation of this information consolidated on a single screen for better understanding) becoming more complete and efficient logistics management. They also become more flexible, allowing the user to develop itself in the way that best suits you, your own reports and charts without the need to request customizations and new developments.
With all these options and flexibility added to the consistent and timely information, the tools of logistics management are becoming powerful tools for Business Intelligence (BI) giving full support to decision making with more accurate and effective results. However, do not just take the tool, you must make proper use for information and necessary corrective work order at critical points in the process and preventively in others, always seeking continuous improvement to achieve different levels of competitiveness in the market.
Full article: http://corporate.canaltech.com.br