Cómo minimizar los errores de picking
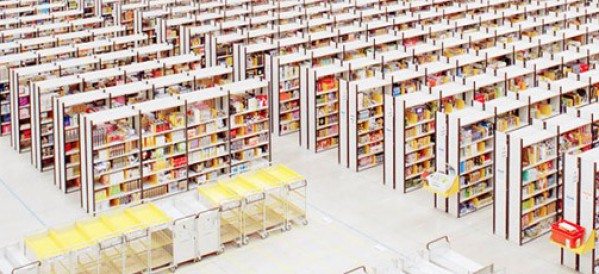
La implantación de un Sistema de Gestión de Almacenes (WMS), utilizando el módulo automático (con lector de código de barras) actúa directamente y puntos críticos en el proceso, tales como la separación de paquetes
En cuanto a los procesos macro de una operación logística – recepción, almacenamiento, recolección y envío – usted puede comprobar si hay errores en el proceso relacionado con la falta de conocimiento y atención.
Los errores debidos a la falta de conocimiento son más fáciles de corregir, ya que pueden ser reparadas mediante la configuración de capacitación y flujos operacionales. El error debido a la falta de atención es más difícil de controlar, ya que se produce debido a las presiones del entorno interno y externo de la organización que el empleado esté expuesto.
En el proceso de picking, los principales errores que se producen están separando el producto incorrecto, manteniendo Imagenes errores Unidad (SKU) diferentes, o diferentes datos logísticos, tales como la fabricación de lote, fecha de caducidad, fecha de fabricación, número de serie, etc. , cantidad incorrecta de fragmentación y artículos “olvidados”. Estos problemas son por lo general el cambio de turno, la salida y retorno del horario de comidas.
La actividad de la cosecha es el almacén más complejo, que tiene un impacto directo en los costos de operación. La pregunta para este escenario es la forma de minimizar los accidentes?
La implantación de un Sistema de Gestión de Almacenes (WMS), utilizando el módulo automático (con lector de código de barras) actúa directamente sobre los errores mencionados anteriormente. Haciendo uso del controlador en el picking, el sistema valida que el mismo artículo que se lee se solicita en el momento de la lectura del código de barras del producto, evitando así suceda separación de objetos incorrectos.
En el proceso automatizado es posible dividir la unidad de lectura unidad realice o consultar la etiqueta del producto y entrando en la cantidad separada. Aún así, con la implementación de WMS, puede realizar la conferencia marítima, que se celebra la lectura de los productos después de la cosecha, validando la cantidad separada es correcta. También puede implementar la conferencia de embarque, control de los productos que se envían en los vehículos.
Por defecto, el sistema requiere que la lectura de códigos de barras del producto se realiza para confirmar la separación. El siguiente proceso, conferencia de despacho, que puede detectar la falta del producto y verificar la dirección que se confirmó la separación sistémicamente, negando la posibilidad de olvidarse de artículos.
Además de ayudar a reducir los errores mencionados anteriormente, el uso de WMS en la gestión de recogida y envío añade a las ganancias de proceso, tales como enrutamiento, la gestión de la realización de las ondas de separación podría ser visto por el grupo o la aplicación individual, la posibilidad de acondicionamiento y coleta montaje en o sobre las conferencias marítimas, más allá del control del número de serie, y la validación de la auditoría recogiendo índice de fragilidad de los productos en el conjunto de transporte durante la paleta de separación.
El proceso también asegura la validación de FIFO, FEFO, fecha de vencimiento, la validación previa de la balanza (física e impuestos) antes de iniciar la separación y la generación de etiqueta de envío. La redundancia de entrada de datos también se inhibe porque existe la posibilidad de integrar aplicaciones mediante facturas electrónicas EDI’se XML.
Es importante destacar que, además del aparato tecnológico, definición de flujo de procesos, definición de roles y responsabilidades en el proceso, la organización física y la determinación del espacio físico para alojar el puesto de picking, después de la conferencia y previas al envío son esenciales para la proceso de selección se lleva a cabo de manera eficiente y eficaz.
También dentro de este tema, es de destacar la atención en los procesos de recepción, manejo e inventario, tratando de disminuir la aparición de roturas (físicas frente divergencia sistémica) de acciones, que son una de las principales causas de pérdida de tiempo en la separación de la actividad.
Artículo completo: http://cio.com.br/