Caminhamos para uma contínua evolução dos armazéns, tanto em seu papel e importância, como em sua infra-estrutura física. Entender a fundo a dinâmica dessa mudança e os impactos no trinômio pessoas-processos-tecnologia será crucial para as empresas manterem-se altamente competitivas em seus respectivos mercados.
Nas décadas de 60, 70 e 80, os armazéns eram vistos como áreas meramente acumuladoras de materiais, com pouca ou nenhuma complexidade. As construções eram simples, sem nenhuma sofisticação, sendo raro encontrarmos pé-direito superior a oito metros, pisos com alta capacidade de resistência (superior a 6 tonf/m2), docas elevadas etc.
A partir da estabilização econômica, alcançada com o Plano Real em meados da década passada, uma importante mudança começa a ocorrer no comportamento dos consumidores brasileiros. Aos poucos, deixamos de fazer as compras mensais (impulsionadas pela espiral inflacionária) que abasteciam a despensa de nossas casas e passamos a comprar menos, porém em mais vezes. Ou seja, nos transformamos em visitantes semanais dos supermercados, cada vez mais atraentes para os consumidores, pelas ofertas semanais e pelos inúmeros “aniversários” realizados ao longo do ano.
O fracionamento das compras por parte dos consumidores provocou uma mudança radical nos armazéns, até então adaptados a lidar apenas com paletes completos e cargas fechadas. Nesse momento, surge a necessidade de “quebrar” os grandes lotes em lotes menores, em frações de paletes, em caixas e até nas unidades primárias. Daí surge a necessidade da criação da área de separação de pedidos (ou picking) e a preocupação com a consolidação das cargas em diferentes tipos de veículos.
A atividade de picking é, atualmente, a de maior representatividade em custos dentre as operações existentes (figura 2).
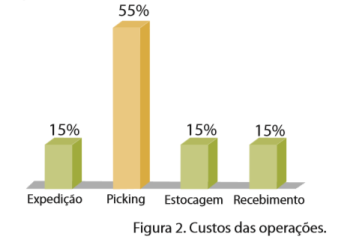
Nessa transição, os armazéns assistiram à verticalização dos estoques, ao uso de equipamentos de movimentação específicos, à formalização dos processos e à especialização da mão-de-obra.
Uma última onda vem sendo vivida desde a virada do século, com a adoção de novas tecnologias de informação (em especial os sistemas WMS – Warehouse Management System), automação da movimentação e estocagem dos materiais, gestão por meio de indicadores de desempenho (KPI – Key Performance Indicators) e práticas incessantes de housekeeping.
Os novos armazéns, rebatizados de Centro de Serviços Logísticos, assumem novas tarefas e passam a ser como minifábricas, atuando intensivamente na montagem de kits promocionais, embalagens especiais, paletização e repaletização etc. Nessa nova realidade, o que entra no armazém não é necessariamente igual ao que sai.
Nos novos armazéns, mais do que simplesmente guardar materiais, há uma preocupação com o fluxo físico de materiais e com as informações.
Os novos armazéns caminham para operações de fluxo contínuo, com cada vez menos estoques, muito próximas das operações de cross-docking, detalhadas a seguir.
A figura 3 ilustra o processo vivido pelos armazéns ao longo dos últimos 30 anos.
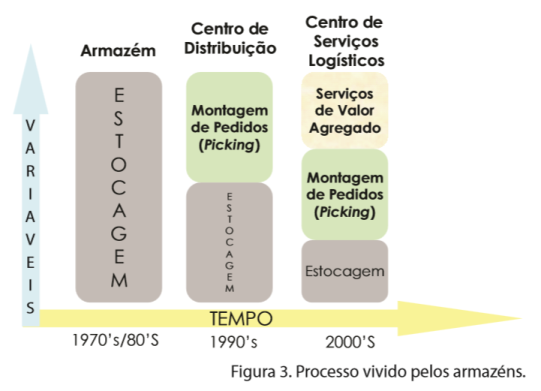
As operações de cross-docking
Cross-docking é uma operação de distribuição na qual os produtos são recebidos, selecionados e encaminhados para outro veículo, e por isso necessita de grande exatidão quanto ao tempo de entrada e saída de produtos.
Além de eliminar altos custos de manuseio de produtos, o investimento em estoques é substancialmente reduzido pela eliminação de múltiplos locais de estocagem.
Operações de cross-docking levam à redução de até 30% quando comparada com uma operação convencional, na qual ocorre a formação de estoques.
A operação de cross-docking, embora simples na teoria, é muito difícil de realizar na prática. Algumas condições operacionais precisam ser atendidas:
- O local de destino do material é conhecido no ato do recebimento;
- Seu cliente está pronto para receber o material imediatamente;
- O produto em suas docas é pré-rotulado;
- Necessidades de controle da qualidade precisam ser mínimas;
- Preferencialmente operação com paletes completos;
- Existir espaço suficiente próximo às docas;
- Entregas disciplinadas no armazém.
São bons candidatos a cross-docking operações que envolvam itens sazonais e itens com altos volumes de venda.
A infra-estrutura física dos armazéns do futuro
Muito diferente dos atuais, os armazéns do futuro deverão conciliar seu tradicional papel na estocagem, mas também deverão viabilizar o rápido fluxo de materiais, na entrada (inbound) e saída (outbound). Essa capacidade de processamento (throughput) será vital para as operações de distribuição.
Como viabilizar funções tão antagônicas em uma mesma estrutura física?
A discussão começa pelo tamanho do armazém. Estudos realizados nos EUA mostram que os armazéns que apresentam melhores indicadores de desempenho têm entre dez mil m2 e 30 mil m2.
Os problemas de controle tendem a aumentar com o tamanho do armazém.
Em armazéns de grande porte, a produtividade é dificultada pelo excesso de movimentação devido a grandes distâncias e má visibilidade do fluxo de trabalho. As dificuldades em comunicação e supervisão possivelmente podem contrabalançar as economias obtidas com grandes volumes de pedido ou por meio de altos níveis de mecanização. Também importante será dimensionar corretamente o formato do armazém, buscando uma proporção adequada entre comprimento (face onde estão localizadas as docas) e largura do armazém (figura 4).
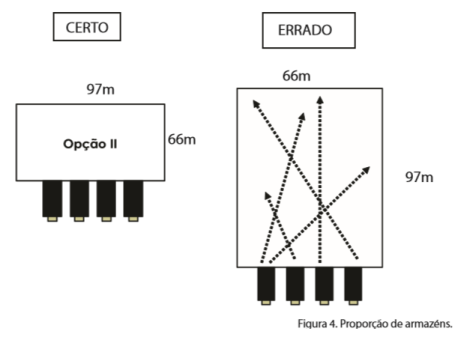
As docas e as áreas de stage terão um papel fundamental nesse novo armazém, no qual se priorizará o fluxo de materiais e não a sua estocagem.
A doca é o meio pelo qual um veículo é colocado no armazém para a carga e descarga. Há dois tipos básicos de configurações de docas para caminhões: de 90º e de 45ª. A doca de 90º precisa de largura menor e profundidade maior do que a doca de 45º. Conseqüentemente, a doca de 90º precisa de menos espaço dentro do armazém e de mais espaço fora do mesmo, para a execução das manobras. Quanto maior a largura da doca, maior será o espaço interno do armazém dedicado a cada doca. Por isso, docas de 90º são mais utilizadas do que as inclinadas.
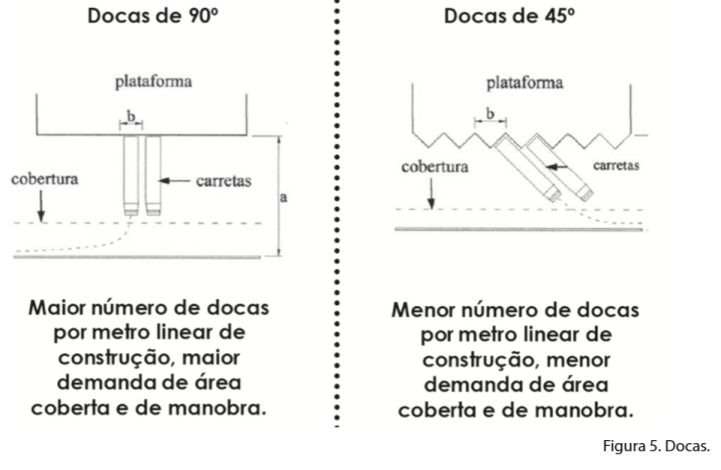
A localização das docas dependerá do layout operacional utilizado, fluxo em “I” ou fluxo em “U”.
Fluxos em “I”, ou fluxos atravessando o armazém, são mais comuns em operações de cross-docking em grandes transportadoras (terminais) e normalmente não possuem áreas para estocagem.
Fluxos em “U” são normalmente utilizados pelas indústrias e segmento varejista.
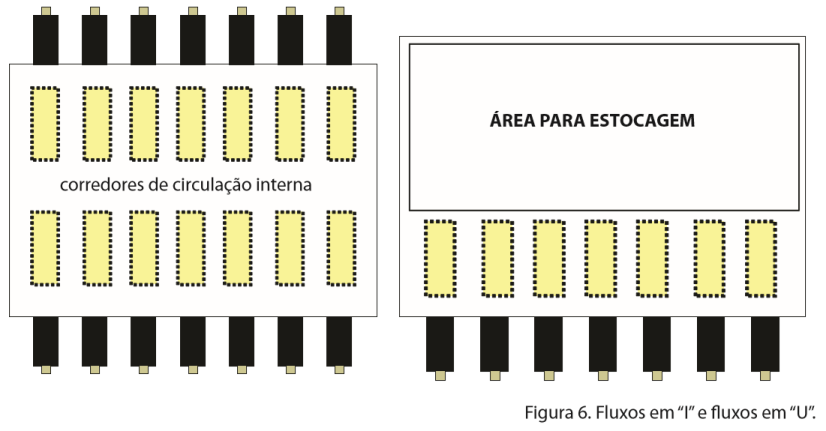
Fluxos em forma de “U” trazem grandes vantagens em relação a outros tipos de projeto:
- Excelente utilização de recursos da doca (equipamentos, funcionários, etc) devido ao fato de que os processo de recebimento e expedição podem compartilhar as portas das docas;
- Facilitação de cross-docking, pois as docas de recebimento e expedição são adjacentes umas às outras;
- Otimização de empilhadeiras, pois as viagens de estocagem e retirada são facilmente combinadas e localizações de estocagem mais perto das docas são as localizações naturais dos items de maior giro.
A quantidade de docas, tradicionalmente dimensionadas numa proporção de uma doca a cada mil m2 de área construída, mudará de forma radical. Será necessário termos pelo menos uma doca a cada 500 m2 de área coberta construída.
As docas deverão estar equipadas com equipamentos para o nivelamento (dock leveler) do armazém com os caminhões, já que não existe um padrão de altura de veículos. Esses equipamentos proporcionam carga e descarga mais rápidas e seguras.
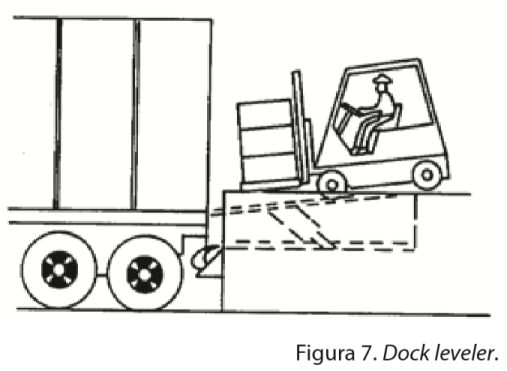
Além disso, a cada doca existente deverá existir, internamente, uma área de stage (espera) correspondente, do tamanho do veículo de carga/descarga utilizado (8,0 a 15,0 metros de comprimento, com largura de 2,5 metros).
O tamanho das áreas de stage-in / stage-out tem relação direta com os tipos de operação de recebimento e expedição:
- Um alto grau de checagem e inspeção aumentará a necessidade de espaço;
- No caso da impossibilidade de controle sobre a chegada dos veículos (dock schedule), uma área suficientemente grande deverá ser dimensionada para suportar os “picos” operacionais ao longo do dia;
- O recebimento de cargas a granel exigirá a paletização dos materiais antes da estocagem;
- Operações de cross-docking exigirão a separação e a consolidação das cargas.
Entre as docas deverá existir um intervalo de 1,5 m a 3,0 m, dependendo do equipamento de movimentação utilizado entre os stages.
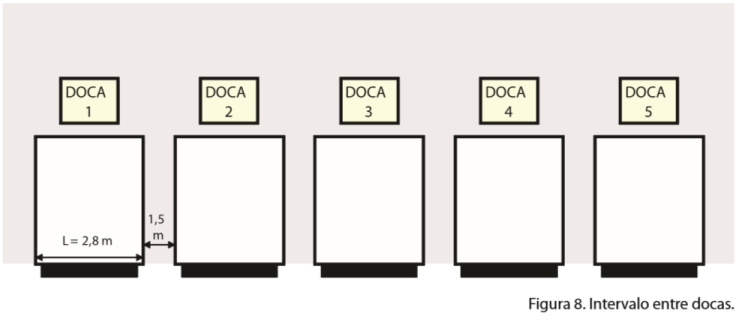
Os caminhões devem entrar na doca de recebimento ou expedição no sentido anti-horário, de modo a permitir que entrem de ré na doca no sentido horário. Isso facilitará a operação para o motorista, que se guiará pelo seu espelho, e não pelo espelho localizado ao lado do passageiro.
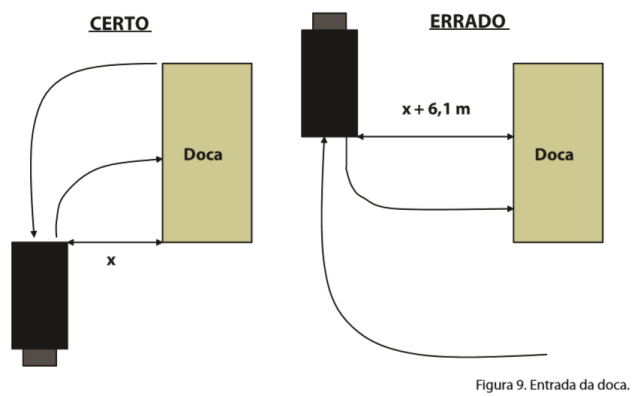
As áreas externas, constituídas do pátio para a manobra e estacionamento de veículos e das ruas para a circulação dos mesmos, também terão um papel fundamental. Normalmente esquecidas ou subdimensionadas, passarão a ter papel importantíssimo, principalmente para viabilizar operações com alta concentração de movimentação na última semana. A profundidade do pátio de manobra variará de 12 m a 20 m, dependendo do comprimento do caminhão.
Quanto à verticalização dos estoques, o tradicional porta-palete, estrutura comumente utilizada pelas empresas, e muitas vezes encarada como a melhor e talvez única solução, dará espaço a um estudo de otimização cúbica, envolvendo a análise de diversas soluções que tratem de forma diferente com a questão de densidade, seletividade e velocidade de processamento. A melhor solução será um mix de soluções e não apenas a solução porta-palete.
WMS – Warehouse Management System
Nem todos necessitam ter um sistema WMS. Seguramente qualquer operação logística se beneficiará do uso dessa importante ferramenta, porém é preciso avaliar os custos com a aquisição e implantação do sistema, comparativamente com os benefícios a serem obtidos.
O WMS é uma ferramenta robusta e complexa, requerendo enormes esforços iniciais, principalmente com a parametrização do sistema e com a constante manutenção dos mesmos, que garantirá o seu perfeito funcionamento. Defensores dos sistemas WMS argumentam que:
- WMS reduzirá os estoques;
- WMS reduzirá os custos com mão-de-obra;
- WMS aumentará o uso da capacidade de estocagem;
- WMS aumentará o serviço ao cliente;
- WMS aumentará o nível de acuracidade dos estoques.
A implantação do WMS, associado à automação da coleta de dados, realmente levará a uma maior acuracidade da informação dos estoques, redução na mão-de-obra e em uma maior capacidade de melhor atender os seus clientes, por meio da redução dos tempos de ciclo. Expectativas quanto à redução de estoques e melhor utilização do espaço cúbico disponível nem sempre são verdadeiras.
Apesar dos benefícios que possam ser obtidos com a redução da mão-de-obra, a decisão de investir ou não em um sistema WMS estará diretamente condicionada ao nível de serviço exigido pelos seus clientes e à capacidade do sistema de preencher as lacunas existentes e agregar valor.
Com um bom sistema WMS, você poderá, por exemplo, praticar o PEPS (primeiro que entra, primeiro que sai), realizar cross-docking, atender pedidos emergenciais, reduzir stockouts, diminuir sensivelmente o risco de obsolescência, disponibilizar informação de estoques em tempo real etc.
Para Operadores Logísticos é uma ferramenta essencial. Para os Embarcadores, deve ser cuidadosamente avaliada, levando em conta aspectos técnicos e financeiros.
Uma vez decidido pela implantação, é necessário tomar um passo anterior: a otimização da infra-estrutura física existente e a revisão dos processos-chave. Sem isso, automatizaremos o que está ruim, portanto, teremos muitas dificuldades em obter os benefícios esperados.
O próximo grande desafio dos armazéns
O avanço da logística reversa deverá se tornar o próximo grande desafio dos profissionais de armazéns. As devoluções, ainda hoje pouco representativas e tratadas com certo descaso, merecerão maior atenção das empresas.
As áreas hoje destinadas ao recebimento, inspeção e triagem dos materiais, ainda pouco relevantes, serão redimensionadas para permitir o correto destino do material devolvido, seja ele a reestocagem, reaproveitamento de componentes, sucateamento etc.
Numa nova realidade, na qual a logística reversa passa a ser representativa em valores e volumes, esqueça o FIFO (First In, First Out) e entenda como funciona o FEFO (First Expired, First Out).
Conclusão
O melhor armazém é, sem dúvida alguma, aquele que não existe. Mas, apesar dos esforços na integração da cadeia de materiais, ECR (Eficient Consumer Response), Just-in-time e Quick Response, a cadeia de materiais nunca será tão perfeitamente coordenada a ponto de eliminar as atividades de movimentação e armazenagem por completo.
Portanto, se os armazéns podem ser considerados um “mal necessário”, precisaremos então saber conviver com eles e extrair o melhor possível, seja em desempenho operacional ou em custos.
Uma visão sistêmica, envolvendo pessoas, processos, tecnologia e infra-estrutura, será imprescindível para alcançarmos um desempenho classe mundial nas operações de movimentação e armazenagem de materiais.
Fonte: Revista Mundo Logística